Share
Pin
Tweet
Send
Share
Send

Every day, more and more radio amateurs use parts and components in their work SMD. Despite the sizes, it’s easier to work with them: you do not need to check the holes in the board, bite off long leads, etc. It is necessary to master the soldering of SMD parts, since it will definitely come in handy.
This master class is not designed for beginners in soldering, but rather for amateurs who solder well but have little difficulty soldering multi-legged chips or controllers.
Will need
- Soldering iron with temperature controller and tip thickness not more than 2 mm.
- Sponge for cleaning the sting.
- Wire ПЩ.
- Tweezers.
- The solder is tubular or otherwise.
- Flux paste.
- Flux is liquid.
This is a minimal set, without expensive soldering stations, hair dryers and desoldering pumps.
Soldering SMD parts with your own hands
So, let's start with the most difficult thing - soldering the controller in the QFP100 package. With chip resistors and capacitors, I think, and so everything is clear. The main rule is: there isn’t much flux or you can’t spoil soldering with flux. Excessive application of flux prevents tin from flowing abundantly over the contact and shorting them. There is also a second minor rule: even a little solder happens a lot. In general, it is necessary to dose and apply it to the sting very carefully so as not to overdo it, otherwise it will flood all at once.
Tinning pad
Experienced electronics do not always perform this step, but on the first couple I recommend it.
It is necessary to tin the board, namely the place where the controller will be soldered. Of course, the site is most likely tinned, especially if the board is made at the factory. But over time, an oxide film appears on the contacts, which may interfere with you.
Heat the soldering iron to operating temperature. Grease the area with flux. We put a little solder on the sting and tin the tracks.

The excess solder is removed with the help of the wire. It perfectly absorbs solder due to the capillarity effect.

Install and align the controller
When the site is ready, it's time to install the controller. There is a trick, most solders install a microcircuit and tweezers align its contacts along the tracks. But to do this is very difficult, since even a slight twitching of the hand tilts the controller a considerable distance.
It will be much easier to do this if you diagonally lubricate the corners with flux paste.

Now install the controller and adjust the tweezers.

As soon as the microcircuit is up, solder the contacts diagonally.

Check if all contacts are in place.
Soldering microcircuit contacts
Here you can already use both liquid and viscous flux. Very abundantly apply it to the contacts.

Wet a drop of solder sting. We clean the excess with a sponge.

And, gently carry out the lubricated contacts.

There is no need to rush.

Removal of excess flux and solder
After soldering all the contacts, it's time to remove the excess solder. Surely a few contacts, but stuck together.
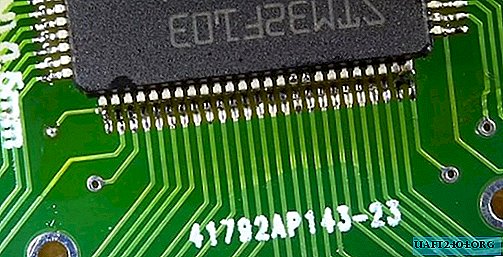

Very abundantly wet the contacts with liquid flux. The soldering iron tip is completely cleaned with a sponge from solder and go through the stuck contacts. Excess solder should be drawn into the sting.
To remove excess flux, use SBS - an alcohol-gasoline mixture mixed 1: 1.
We urinate abundantly.

And wipe.

Be sure to watch the video, where the movement of the soldering iron and all the manipulations are clearly visible.
Share
Pin
Tweet
Send
Share
Send